
The OPTILUX LED-based dynamic light displays are at the heart of the surface inspection solutions developed by VIRELUX.
The curved structured light generator technology allows the development of dedicated metrology and surface inspection stations.
The modular display systems are also a novel stand-alone solution:
They can be used as dynamic displays for audit stations, as well as dedicated, curved displays for quality inspection.
The OPTILUX light generators improve visual acuity through the use of a dynamic display mode, capable of rendering horizontal and vertical stripes with a sinusoidal light transitions.
-
Dynamic & structured control of displayed light
-
Continuous display curvature
-
Adjustable stripes width
-
V & H direction of stripes display
-
Sinusoidal grey-level stripe transitions
-
Simple and modular scalability
-
Adjustable luminosity, contrast, color & temperature settings
-
Designed for automated, industrial-grade defect detection
Designed for appearance quality &
paint defects inspection
This feature fundamentally increases the topography visibility of defaults in the perceived quality, significantly reducing operator fatigue and discomfort during inspections.
Furthermore, the continuous curvature of the dynamic displays allows the generation of regular & uninterrupted light patterns (adjustable in width) with progressive grey-level transitions, improving detection capabilities.
The OPTILUX displays are also adapted to do automotive inline paint quality control inspections. You may find further information about this application on our dedicated page: Automotive Paint Inspection
Quality inspections are often carried out In poor lighting conditions. This means that the work requires more time and effort, while faults or imperfections are often missed. To check surface and irregularities the human eye capacity are directly affected by lighting condition . Efficient quality control inspection can only be performed in optimal ambient conditions.
The right light affects employee performance and impact the quality of the final product, making it an essential consideration for any company. When it comes to surface-check lighting, it is therefore vital that the lighting solution meets the requirements of the materials reflectivity and finishes of automotive A class surfaces requirement.
Paint inspection in production lines, aimed at minor default detection on car bodies, is a very demanding task of key importance. The reflected surface light directly affects the visual inspection performance, with current static solutions requiring extensive levels of concentration and attention to compensate for their technological limitations.
The OptiLux solution improves visual acuity through the use of a dynamic display, capable of rendering horizontal and vertical stripes with a sinusoidal light transition. This feature significantly increases the topography visibility of defaults in the paint process and significantly reduces operator fatigue and discomfort.
Furthermore, the continuous curvature of the OptiLux light source allows the generation of regular & uninterrupted reflective light patterns, adjustable in width, with progressive grey-level transitions, further heightening the detection ease.
Linear light box versus Curved LED Light Generators

Visual inspection for irregularities in reflected light
Audit station and static light tunnel for visual inspection


Regular and continuous light reflected with progressive transitions
Inefficient light distribution due to discontinued static light sources
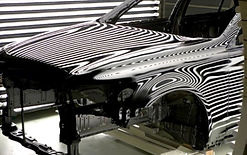
Paint inspection in production lines, aimed at minor default detection on car bodies, is a very demanding task of key importance. The reflected surface light directly affects the visual inspection performance, with current static solutions requiring extensive levels of concentration and attention to compensate for their technological limitations.
The OptiLux solution improves visual acuity through the use of a dynamic display, capable of rendering horizontal and vertical stripes with a sinusoidal light transition. This feature significantly increases the topography visibility of defaults in the paint process and significantly reduces operator fatigue and discomfort.
Furthermore, the continuous curvature of the OptiLux light source allows the generation of regular & uninterrupted reflective light patterns, adjustable in width, with progressive grey-level transitions, further heightening the detection ease.
Application in paint defect inspection
The basic principle is deflectometry, similar to a claim adjuster’s procedure. In contrast to a human observer, the distortion after reflection of a lines pattern on the vehicle’s surface is observed.
In one case it is done subjectively by eyes in the second case (our technology) it is done by camera trough perfectly controlled environment allowing absolute measurements. We then go from subjectivity to objectivity (metrology).
The distortion are caused by the vehicle shape and locally by the defects. By computing analysis of the reflection, even the smallest surface defects can be reliably detected and quantified to deliver an objective auto calibrated measurement of the defects on metric scale.
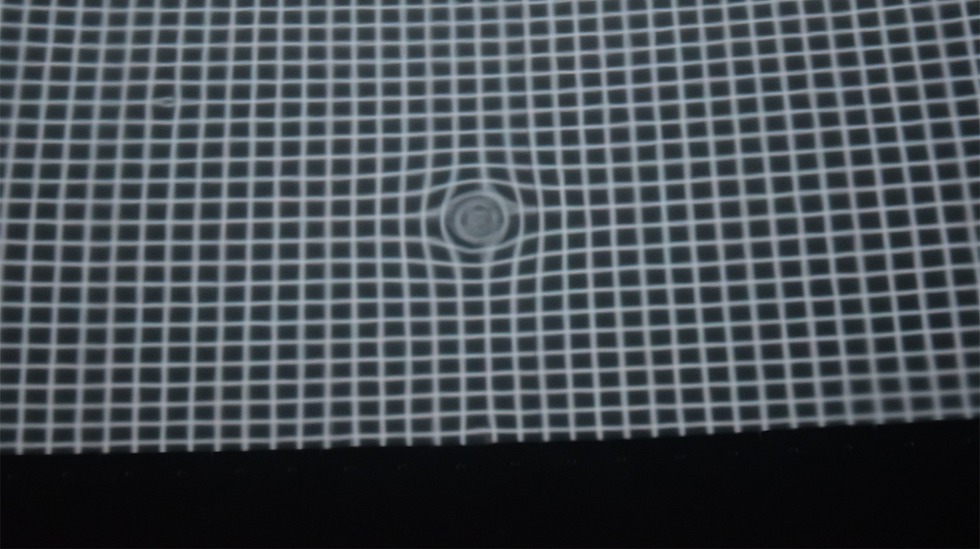
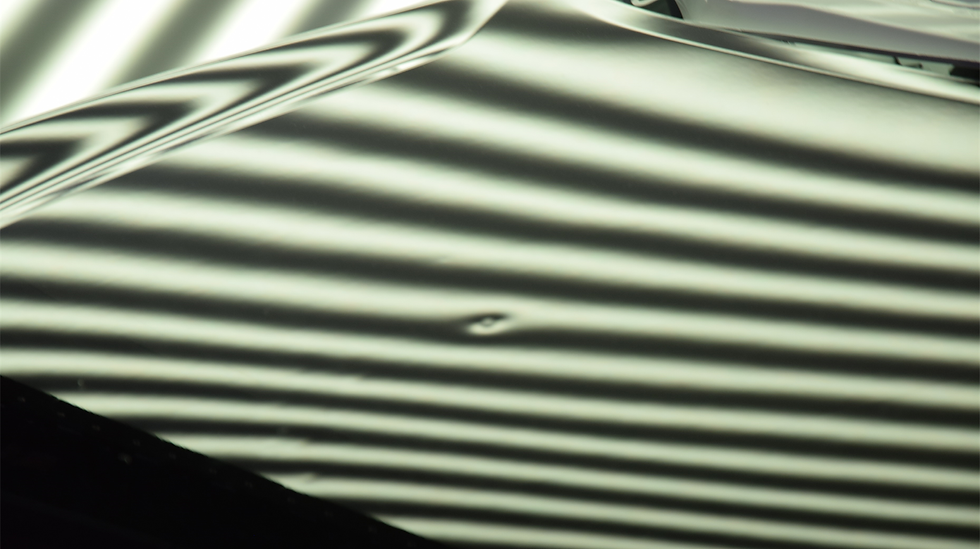

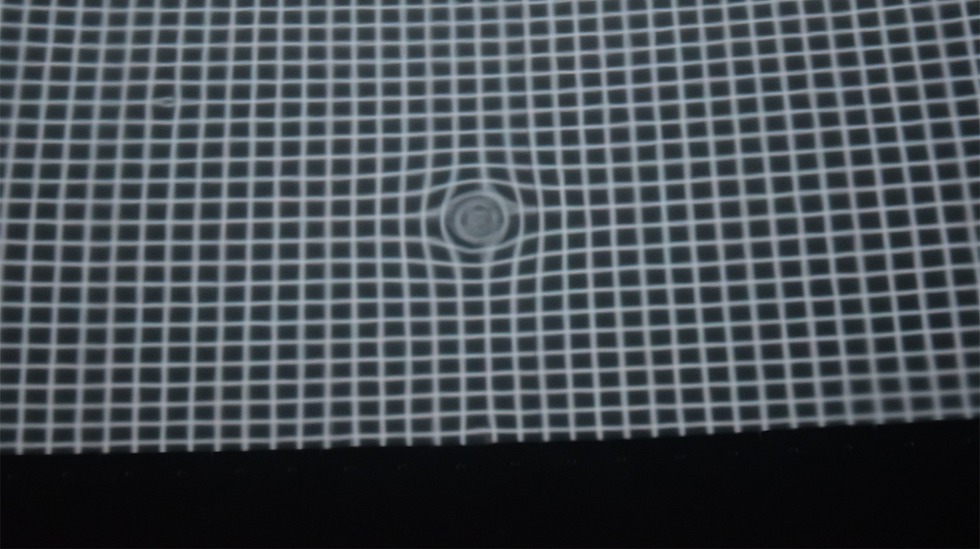
Main benefits over traditional solutions

A sinusoidal light transition significantly improves defect detection sensitivity.
The width of the sinusoidal patterns can be configured
The enveloping shape of display eliminates the need for light boxes on the floor-which tend to blind operators-as it reflects light even on the lowest parts of the car.
The distance between the car and the screen remains constant.
The curved display allows for a better spread of the reflected light onto the inspected car, due to its cotinue curved shape
The OPTILUX dynamic light tunnels allow for denser black & white or color stripes, compared to regular static light tunnels.
This further improves defect detection sensitivity, in addition to the sinusoidal pattern.
The dynamic light source allows the display of vertical, horizontal of angular lines or grids, the modification of the step of the displayed fring pattern, and the generation of sinusoidal light profile.
These parameters are essential to enable an optimal defect detection environment.
It is also possible to reduce the step of the fringe pattern and to access the light source settings (color, color temperature, refresh rate, luminosity, contrast,...)
A dynamic light source is the preamble to an automated defect measurement system.
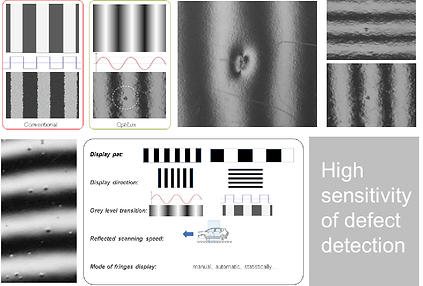
© 2020 VIRELUX Inspection Systems s. à r. l. | 126 avenue Charlotte, L-4531 Differdange, Luxembourg | info@virelux.com | (+352) 621 184 041